工具は工作機械を加工する上で重要な部品の一つです。科学技術の発展に伴い、工具は元の合金工具から最も一般的に使用されるコーティング工具に変わりました。超硬工具やハイス工具の再研磨と再コーティングは現在一般的なプロセスです。工具の再研磨や再コーティングの費用は、新しい工具の製造コストのほんの一部にすぎませんが、工具の寿命を延ばし、製造コストを削減できます。再研磨加工は特殊工具や高価な工具の代表的な処理方法です。再研磨または再コーティングが可能な工具には、ドリルビット、フライス、ホブ、成形工具などがあります。
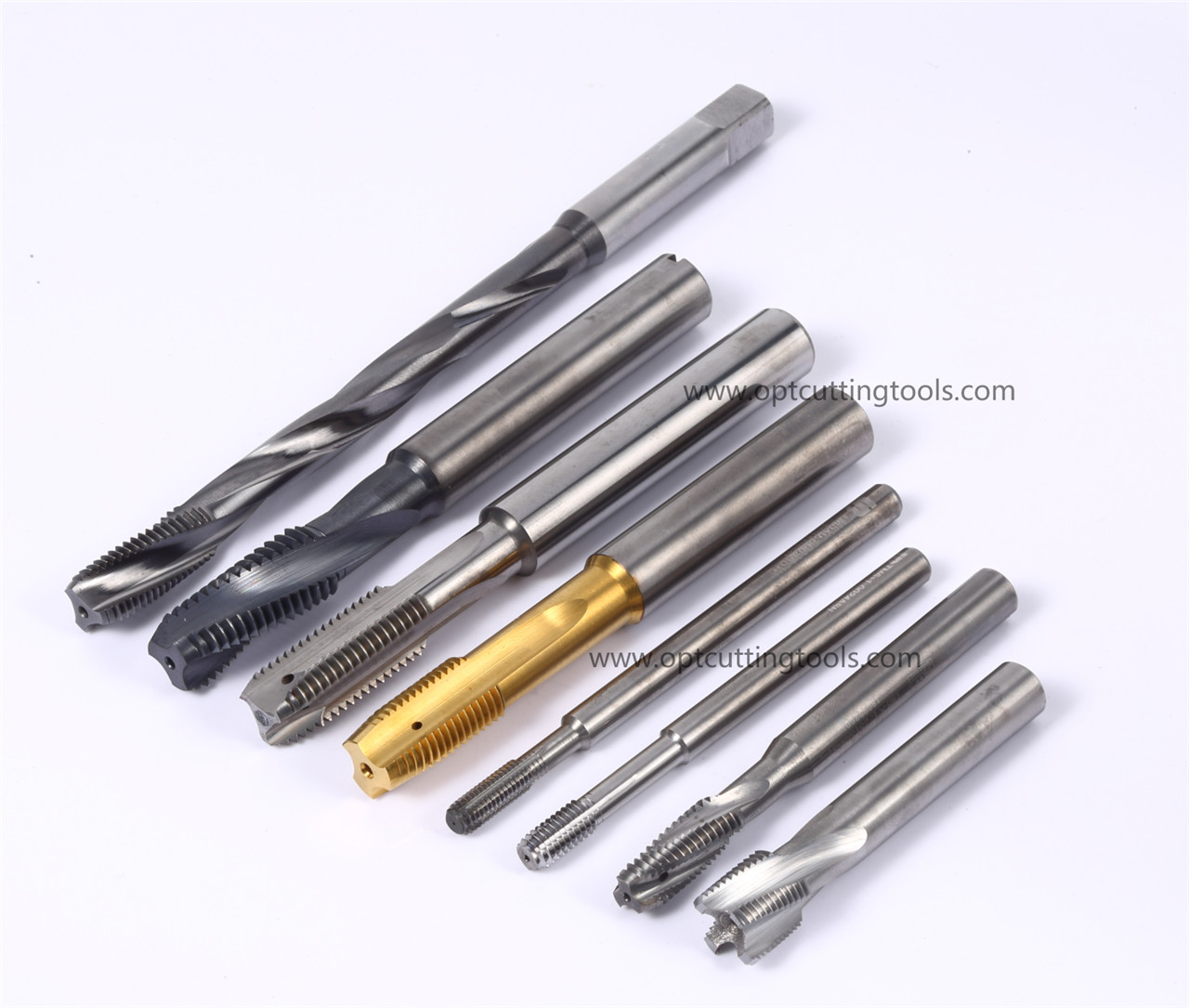
工具の再研磨
ドリルやフライスの再研磨工程では、刃先を研削して元の被膜を除去する必要があるため、使用する砥石には十分な硬度が必要です。再研磨による刃先の前処理は非常に重要です。工具の再研磨後に元の切れ刃の幾何学的形状が完全かつ正確に保持されることを保証する必要があるだけでなく、PVD コーティングされた工具が再研磨に対して「安全」でなければならないことも必要です。したがって、無理な研削加工(荒研削や空研削など、高温により工具表面にダメージを与えるような加工)は避ける必要があります。
コーティングの除去
工具を再コーティングする前に、元のコーティングをすべて化学的方法で除去することができます。化学的除去方法は、複雑な工具 (ホブやブローチなど) や複数回の再コーティングを行った工具、コーティングの厚さによって問題が発生した工具によく使用されます。コーティングを化学的に除去する方法は、超硬合金基材に損傷を与えるため、通常、高速度鋼工具に限定されます。コーティングを化学的に除去する方法では、超硬合金基材からコバルトが濾過され、その結果、表面に多孔性が生じます。基材、気孔の形成、および再コーティングの困難さ。
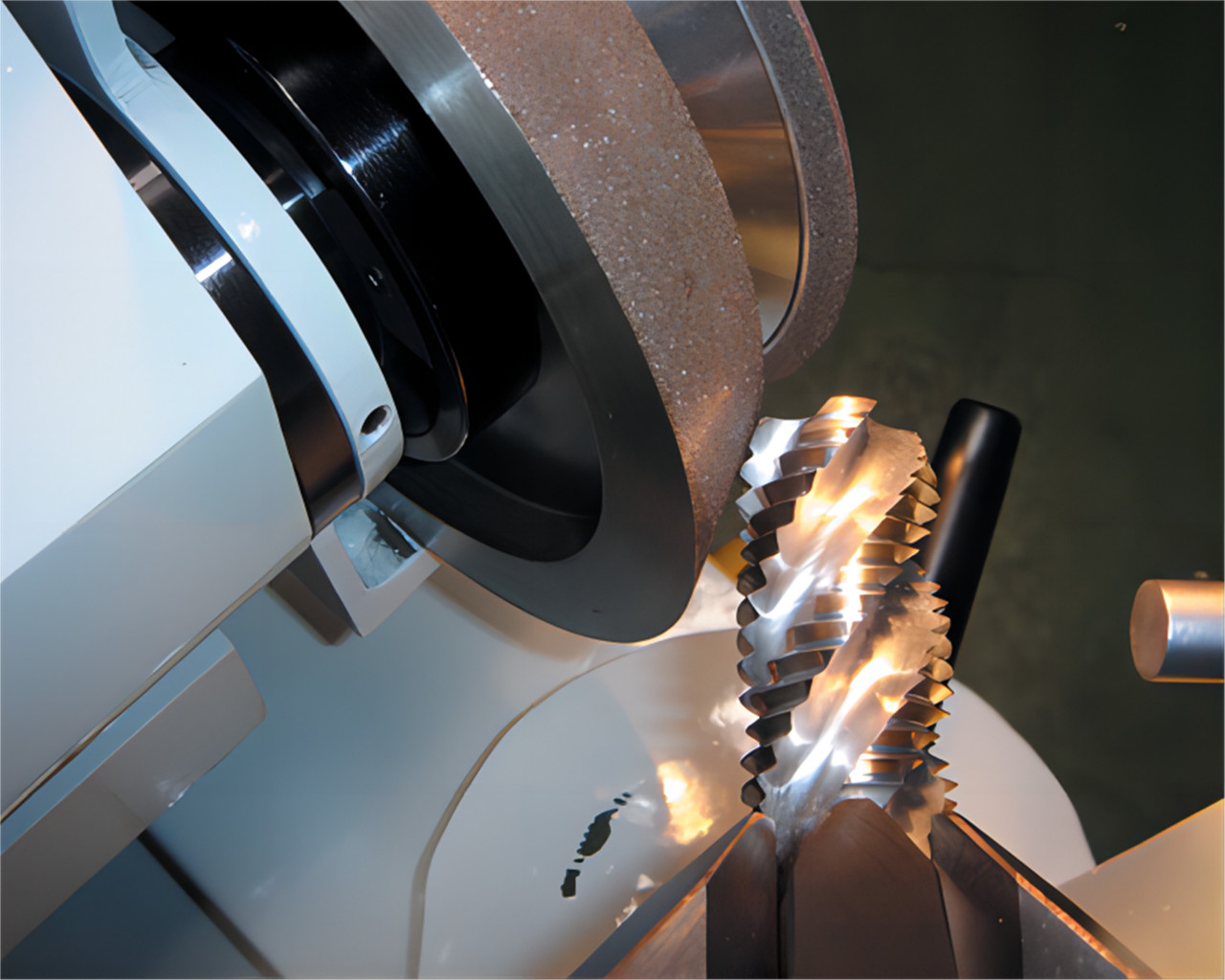
「高速度鋼の硬質皮膜の腐食除去には、化学的除去方法が推奨されます。」超硬合金マトリックスにはコーティングに含まれる化学成分と同様の化学成分が含まれているため、化学除去溶剤は高速度鋼マトリックスよりも超硬合金マトリックスを損傷する可能性が高くなります。
さらに、PVD コーティングの除去に適した特許取得済みの化学的方法がいくつかあります。これらの化学的方法は、被膜除去液と超硬合金マトリックスとの間にわずかな化学反応が生じるだけであるが、現在では広く使用されていない。さらに、コーティングを洗浄するには、レーザー加工、研磨ブラストなどの他の方法もあります。化学的除去方法は、表面コーティングの除去を均一に良好に行うことができるため、最も一般的な方法です。
現在、一般的な再コーティングプロセスは、再研磨プロセスを通じて工具の元のコーティングを除去することです。
再塗装の経済性
最も一般的な工具コーティングは、TiN、TiC、TiAlN です。他の超硬窒素/炭化物コーティングも適用されていますが、あまり一般的ではありません。PVD ダイヤモンドコーティングされた工具は、再研磨および再コーティングも可能です。再コーティングプロセス中、重要な表面への損傷を避けるためにツールを「保護」する必要があります。
これはよくあるケースです。コーティングされていない工具を購入した後、ユーザーは再研磨が必要なときにコーティングしたり、新しい工具や再研磨工具に異なるコーティングを適用したりできます。
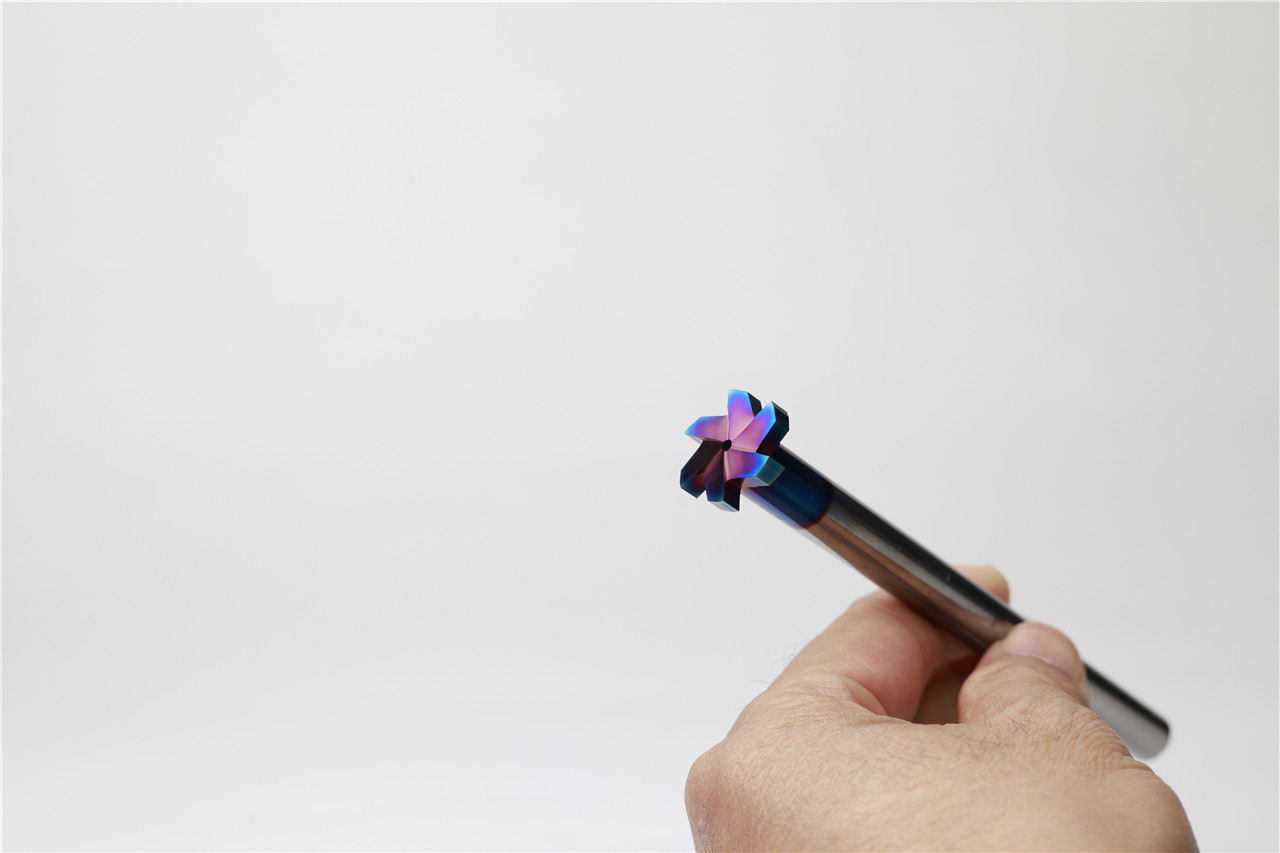
再塗装の限界
工具を何度も再研磨できるのと同じように、工具の刃先にも何度もコーティングを施すことができます。工具の性能を向上させる鍵は、再研磨された工具の表面に密着性の高いコーティングを得ることが重要です。
工具の種類や加工で使用される切削パラメータによっては、刃先を除いて工具表面の残りの部分は、工具を研削するたびにコーティングまたは再コーティングする必要がない場合があります。ホブやブローチは再塗装の際に元の塗膜を全て除去しなければ工具の性能が低下してしまう工具です。応力による接着の問題が顕著になる前に、古いコーティングを除去せずにツールを数回再コーティングすることができます。PVD コーティングには金属の切断に有利な残留圧縮応力がありますが、この圧力はコーティングの厚さが増すにつれて増加し、一定の限界を超えるとコーティングが剥離し始めます。旧塗膜を除去せずに再コーティングを行う場合、工具外径に厚みが加わります。ドリルビットの場合、穴の直径が大きくなることを意味します。したがって、コーティングの追加厚さが工具の外径に及ぼす影響と、両者が加工穴径の寸法公差に及ぼす影響を考慮する必要があります。
ドリルビットは、古いコーティングを除去せずに5〜10回コーティングすることができますが、その後は深刻なエラーの問題に直面します。スペックツール社副社長のデニス・クライン氏は、コーティングの厚さは±1μmの誤差範囲内であれば問題ないと考えていた。ただし、誤差が0.5~0.1μmの範囲にある場合には、膜厚の影響を考慮する必要があります。コーティングの厚さが問題にならない限り、再コーティングおよび再研磨された工具は、元の工具よりも優れた性能を発揮する可能性があります。
投稿日時: 2023 年 2 月 24 日