現代の科学技術の発展に伴い、高硬度のエンジニアリング材料がますます多く使用されていますが、従来の旋削技術では能力が不足しているか、一部の高硬度材料の加工はまったく実現できません。コーティングされた超硬、セラミック、PCBN、およびその他の超硬工具材料は、高い高温硬度、耐摩耗性、熱化学的安定性を備えており、高硬度材料の切削に最も基本的な前提条件を提供し、生産において大きな利点をもたらしています。超硬工具に使用される材質と工具構造、幾何学的パラメータは、ハードターニングを実現するための基本要素です。したがって、安定したハードターニングを実現するには、超硬工具材料を選択し、合理的な工具構造と幾何学的パラメータを設計する方法が重要です。
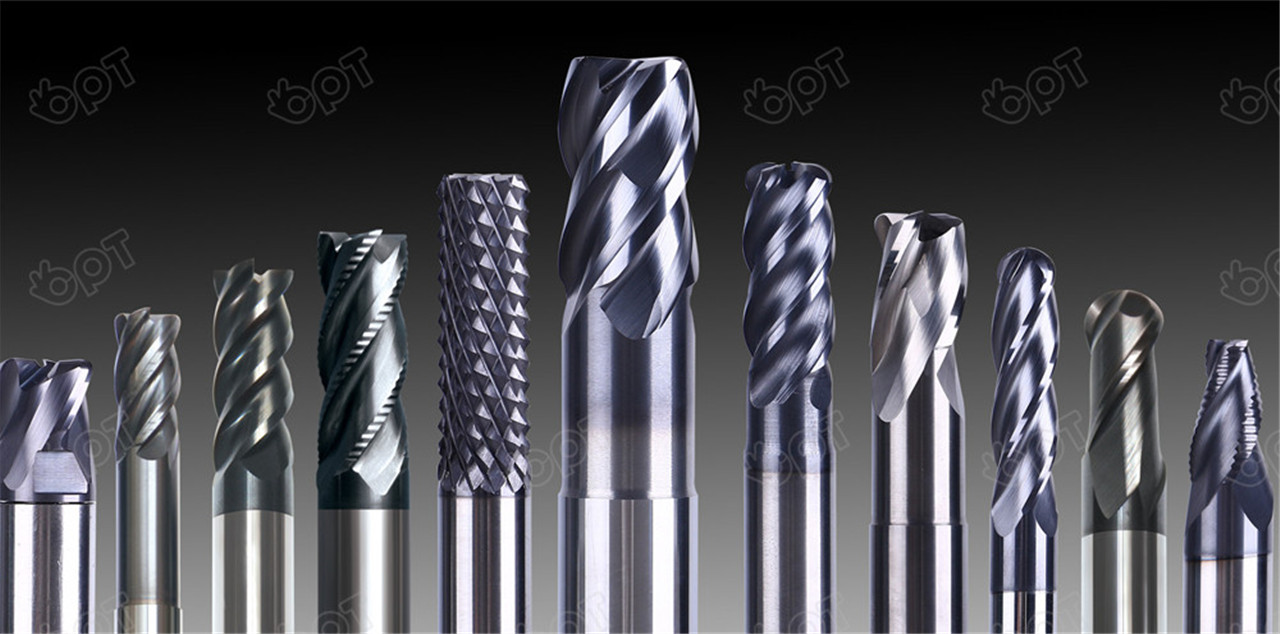
(1) コーティング超硬合金
靱性の良い超硬工具に耐摩耗性の良いTiN、TiCN、TiAlN、Al3O2を1層以上コーティングし、膜厚は2~18μmです。通常、コーティングの熱伝導率はツール基板やワーク材料よりもはるかに低いため、ツール基板の熱効果が弱まります。一方、切削加工時の摩擦と密着性を効果的に改善し、切削熱の発生を低減します。
PVD コーティングには多くの利点がありますが、Al2O3 やダイヤモンドなどの一部のコーティングは CVD コーティング技術を採用する傾向があります。Al2O3は耐熱性と耐酸化性に優れたコーティングの一種で、切削時に発生する熱を特定の工具から切り離すことができます。CVD コーティング技術は、さまざまなコーティングの利点を統合して、最高の切断効果を実現し、切断のニーズを満たすこともできます。
コーティング超硬工具は超硬工具に比べて強度、硬度、耐摩耗性が大幅に向上しています。HRC45~55の硬度のワークを旋削加工する場合、低コストのコーティング超硬合金で高速旋削を実現します。近年、メーカーによってはコーティング材料の改良などによりコーティング工具の性能が向上しています。たとえば、米国と日本の一部のメーカーは、スイスの AlTiN コーティング材と新しいコーティング特許技術を使用して、HV4500 ~ 4900 の硬度を持つコーティングブレードを製造しており、HRC47 ~ 58 のダイス鋼を 498.56m/min の速度で切断できます。 。旋削温度が1500~1600℃まででも硬度は低下せず、酸化もありません。一般的なコーティング刃に比べて刃寿命が4倍あり、コストも30%安く、密着性も良好です。
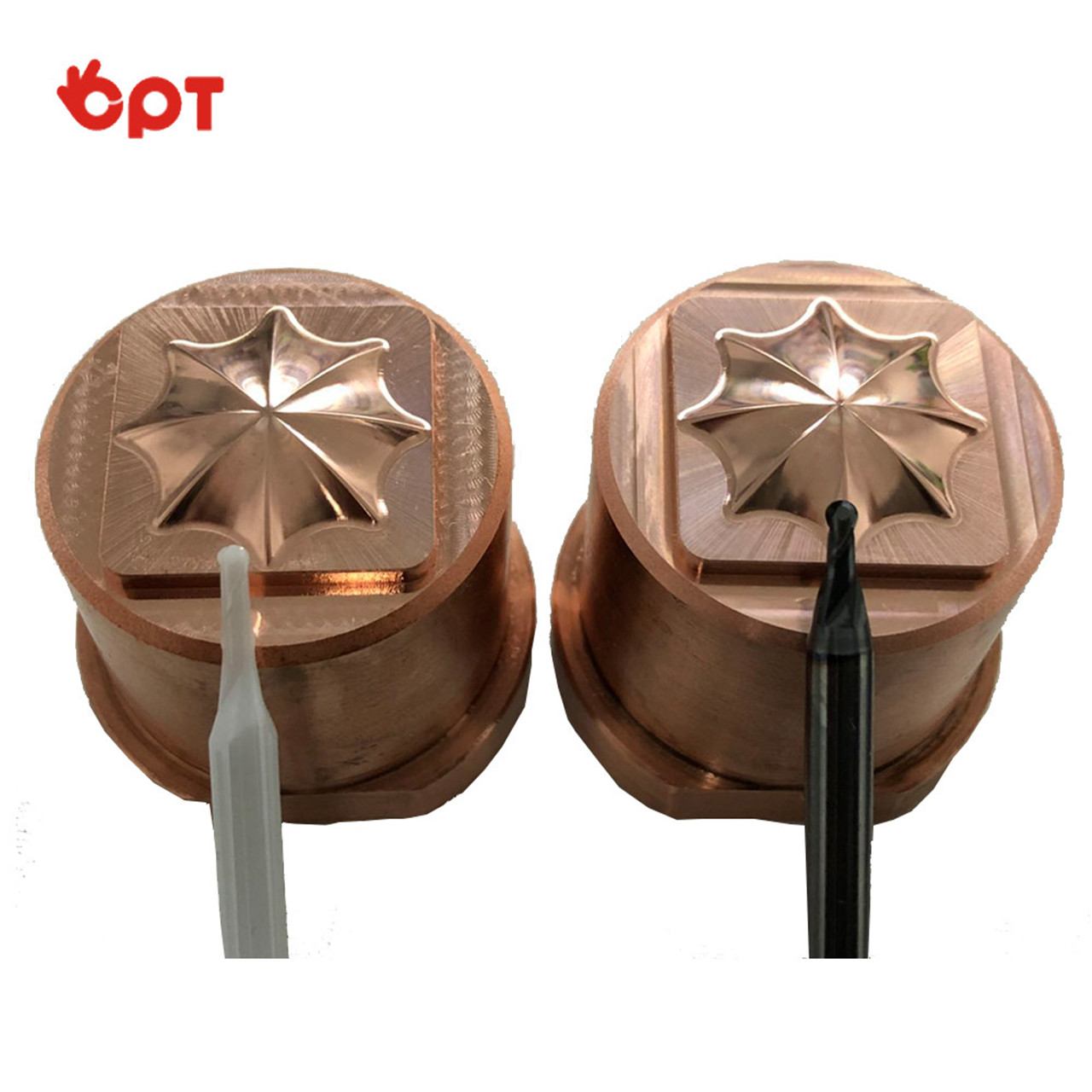
(2) セラミックス材料
セラミック工具材料は、その組成、構造、プレス加工の継続的な改良、特にナノテクノロジーの発展により、セラミック工具の高硬度化が可能になりました。近い将来、セラミックスはハイス、超硬に次ぐ第三の切削革命を起こすかもしれません。セラミック工具は、高硬度(HRA91~95)、高強度(曲げ強度750~1000MPa)、耐摩耗性、化学的安定性、耐溶着性、低摩擦係数、低価格という利点を持っています。それだけでなく、セラミック工具は高温硬度も高く、1200℃でHRA80に達します。
通常の切削においては、セラミック工具は耐久性が非常に高く、超硬工具に比べて2~5倍の切削速度が得られます。特に高硬度材の加工、仕上げ加工、高速加工に最適です。硬度HRC65までの各種焼き入れ鋼、焼き入れ鋳鉄の切断が可能です。一般的に使用されるのは、アルミナベースのセラミック、窒化ケイ素ベースのセラミック、サーメット、ウィスカー強化セラミックです。
アルミナベースのセラミック工具は、超硬合金よりも高い赤色硬度を持っています。一般に、刃先は高速切削条件下でも塑性変形を起こしませんが、強度と靭性は非常に低いです。靭性と耐衝撃性を向上させるために、ZrO または TiC と TiN の混合物を添加することができます。別の方法は、純粋な金属または炭化ケイ素のウィスカーを追加することです。高い赤色硬度に加えて、窒化ケイ素ベースのセラミックは優れた靭性も備えています。アルミナ系セラミックスと比較すると、鋼の加工時に高温拡散が起こりやすく、工具の摩耗が悪化するという欠点があります。窒化ケイ素ベースのセラミックは、主にねずみ鋳鉄の間欠旋削およびフライス加工に使用されます。
サーメットは炭化物ベースの材料の一種で、TiC が主な硬質相 (0.5 ~ 2 μm) です。Co または Ti バインダーと結合しており、超硬工具に似ていますが、親和性が低く、摩擦が良好で、優れた特性を持っています。耐摩耗性。従来の超硬合金に比べて高い切削温度に耐えることができますが、超硬合金のような耐衝撃性、重切削時の靱性、低速・大送り時の強さには劣ります。
(3) 立方晶窒化ホウ素(CBN)
CBNはダイヤモンドに次ぐ硬度と耐摩耗性を有し、高温硬度に優れています。セラミックスと比較すると、耐熱性、化学的安定性は若干劣りますが、耐衝撃性、耐粉砕性は優れています。高硬度鋼(HRC ≥ 50)、パーライトねずみ鋳鉄、チル鋳鉄、超合金の切削に広く適用できます。超硬工具と比べて切削速度を1桁向上させることができます。
CBN 含有量が高い複合多結晶立方晶窒化ホウ素 (PCBN) 工具は、高い硬度、優れた耐摩耗性、高い圧縮強度、優れた衝撃靱性を備えています。欠点は、熱安定性が低く、化学的不活性度が低いことです。耐熱合金、鋳鉄、鉄系焼結金属の切断に適しています。PCBN工具中のCBN粒子の含有量は低く、セラミックスを結合剤として使用したPCBN工具の硬度は低いですが、前者の材料の低い熱安定性と低い化学的慣性を補い、高硬度鋼の切断に適しています。
ねずみ鋳鉄や焼き入れ鋼を切削する場合は、セラミック工具とCBN工具の選択が可能です。このため、どちらを選択するかを決定するには、費用対効果と処理品質の分析を実行する必要があります。切削硬度がHRC60より低く、送り速度が小さい場合にはセラミックツールの方が適しています。PCBN工具はHRC60以上の硬度のワークの切削、特に自動加工や高精度加工に適しています。また、PCBN 工具で切削した後のワーク表面の残留応力も、同じ逃げ面摩耗条件下ではセラミック工具に比べて比較的安定しています。
PCBN ツールを使用して硬化鋼を乾式切断する場合は、次の原則にも従う必要があります。工作機械の剛性が許す条件下で、可能な限り大きな切り込み深さを選択して、切断領域で発生する熱を和らげることができます。エッジの前部の金属を局所的に除去し、PCBN ツールの摩耗を効果的に軽減します。さらに、小さな切削深さを使用する場合は、PCBN ツールの熱伝導率が低いため、切削領域の熱が拡散するのが遅すぎる可能性があり、せん断領域でも明らかな金属軟化効果が生じる可能性があることも考慮する必要があります。刃先の磨耗。
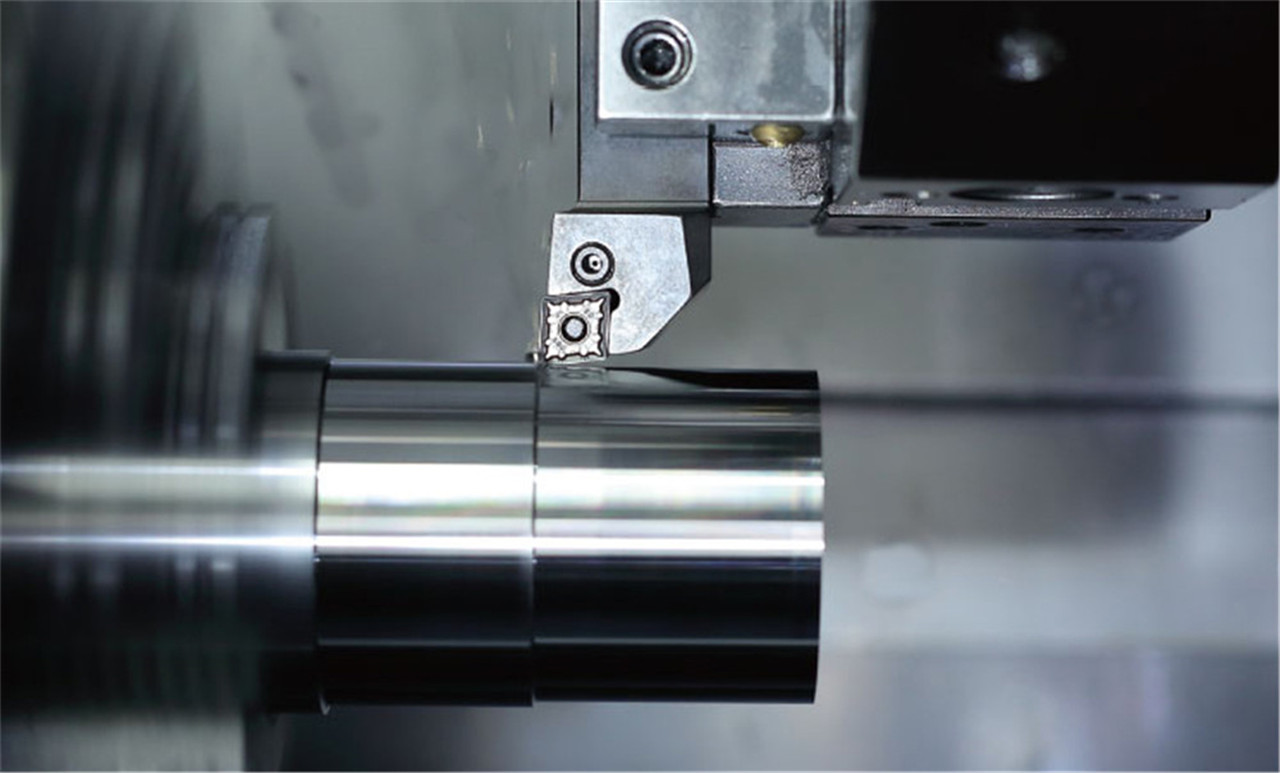
2. 超硬工具の刃構造と幾何学的パラメータ
工具の形状と幾何学的パラメータを合理的に決定することは、工具の切削性能を最大限に発揮するために非常に重要です。工具強度に関しては、丸、100°ひし形、四角形、80°ひし形、三角、55°ひし形、35°ひし形、と高刃から低刃までの様々な刃形状の工具先端強度を示します。刃の材質を選定した後、最も強度の高い刃の形状を選定します。硬質旋削ブレードもできるだけ大きいものを選択し、荒加工は円形で先端円弧半径の大きなブレードを使用して行う必要があります。先端円弧半径は仕上げ時約0.8μ~m程度です。
硬化鋼チップは赤色で柔らかいリボン状で、非常に脆く、壊れやすく、結合しません。焼入れ鋼の切削面は高品質であり、一般に切りくずが堆積しませんが、切削抵抗は大きく、特にラジアル切削抵抗は主切削抵抗よりも大きくなります。したがって、ツールは負の前面角度 (go ≥ - 5 °) と大きな背面角度 (ao=10°~15°) を使用する必要があります。主な振れ角は工作機械の剛性に依存し、一般的には45°~60°となり、ワークと工具のビビリを低減します。
投稿日時: 2023 年 2 月 24 日